Harvester chipper chainsaw chains represent a pinnacle of engineering and design, meticulously crafted to achieve precision cuts in the demanding world of timber harvesting. Behind their seemingly simple construction lies a sophisticated science that enables these chains to deliver accurate, clean, and efficient cuts. Let's delve into the science that underpins the precision cuts achieved by harvester chipper chainsaw chains:
1. Tooth Geometry and Cutting Angles:
The foundation of precision cutting lies in the tooth geometry and cutting angles of the chain. Each tooth is meticulously designed to have specific cutting angles, rake angles, and clearance angles. These angles determine how the chain engages with the wood, effectively slicing through the fibers without excessive resistance. Properly designed angles minimize friction, reduce splintering, and contribute to a smooth, precise cut.
2. Chain Pitch and Gauge:
Chain pitch refers to the distance between successive chain rivets, while chain gauge refers to the thickness of the drive links. The pitch and gauge of a harvester chipper chainsaw chain are meticulously engineered to match the size and power of the chainsaw or harvester machine. Properly matched pitch and gauge contribute to even force distribution and prevent binding during cutting, ensuring a consistent and accurate cut.
3. Material Selection:
The choice of materials plays a critical role in the performance of harvester chipper chainsaw chains. High-quality steel alloys are used to create durable teeth that resist wear and maintain sharpness over extended periods of use. Advanced materials with high hardness and toughness ensure that the chain can withstand the demands of cutting through dense wood without premature wear.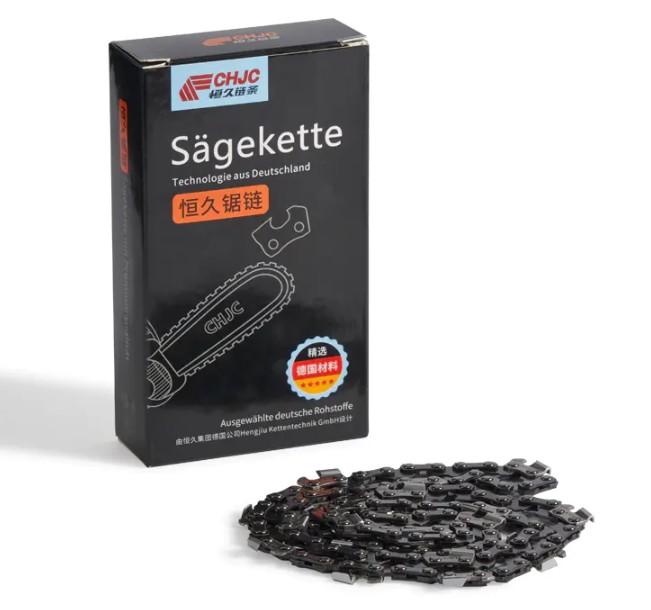
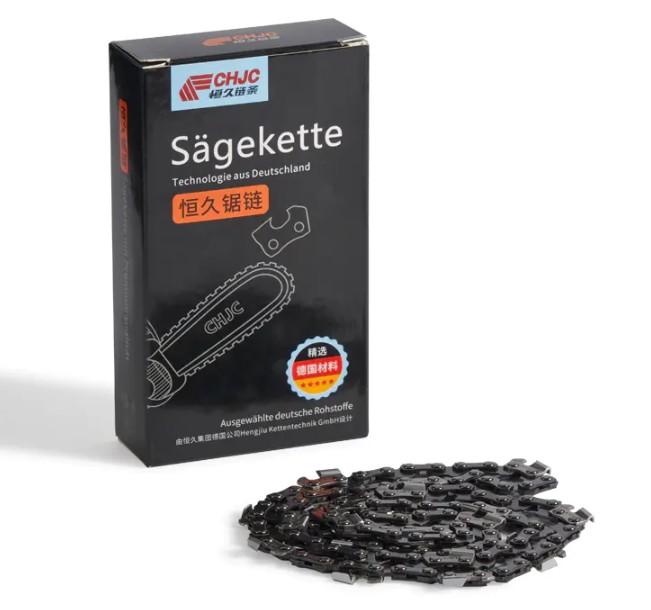
4. Heat Treatment and Hardening:
To ensure durability and longevity, the chain's teeth undergo heat treatment and hardening processes. Heat treatment involves controlled heating and cooling to enhance the steel's mechanical properties, such as hardness and toughness. This process ensures that the teeth remain sharp and resilient even in challenging cutting conditions.
5. Anti-Vibration Mechanisms:
Vibration can negatively impact cutting accuracy. Harvester chipper chainsaw chains often incorporate anti-vibration features, such as dampeners between the drive links. These mechanisms absorb and dampen vibrations, enhancing operator control and contributing to precise cutting.
6. Lubrication and Cooling:
Proper lubrication is crucial to reducing friction, heat buildup, and wear during cutting. Harvester chipper chainsaw chains are designed to channel lubricating oil to the cutting edges, ensuring smooth operation and preventing overheating. Effective lubrication contributes to accurate and efficient cutting performance.
7. Tensioning and Chain Stability:
Maintaining proper chain tension is essential for precision cuts. Tensioning mechanisms ensure that the chain remains stable during operation, preventing buckling or excessive vibrations that could compromise cutting accuracy.
8. Manufacturing Precision:
The manufacturing process of harvester chipper chainsaw chains involves high precision and quality control. Computer-controlled machining and inspection techniques ensure uniformity in tooth geometry, pitch, and other critical dimensions, contributing to consistent cutting performance.
9. Advanced Manufacturing Techniques:
Modern manufacturing techniques, such as laser cutting and CNC machining, enable intricate tooth designs and precise manufacturing tolerances. These techniques contribute to the creation of chains with optimized cutting performance.
In essence, the science behind harvester chipper chainsaw chains revolves around a meticulous understanding of material properties, cutting dynamics, and engineering principles. Every aspect of chain design, from tooth geometry to material selection, is carefully considered to achieve the ultimate goal: mastering precision cuts in timber harvesting. Through the application of advanced science and technology, these chains stand as a testament to human ingenuity and our ability to shape tools that seamlessly blend innovation and functionality.